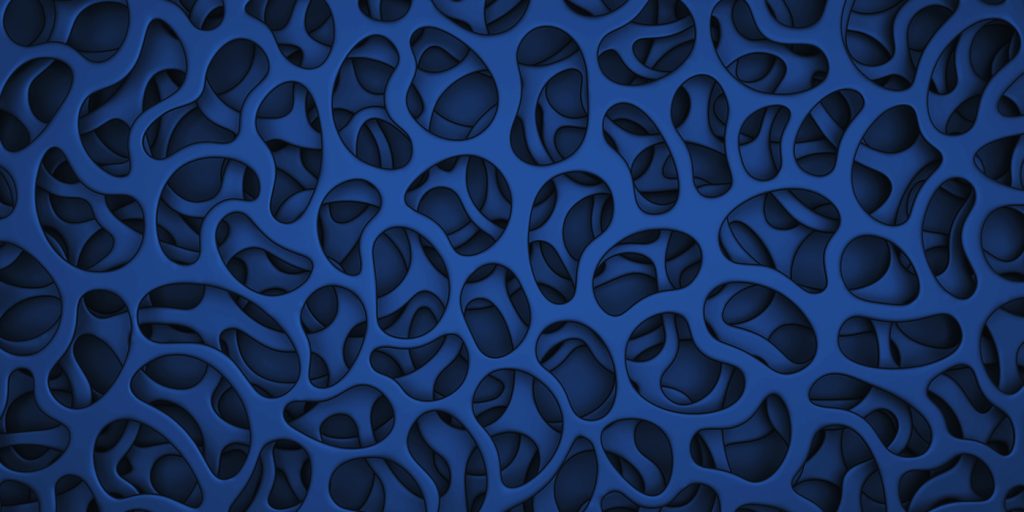
Controlled pore glass (CPG) is a high-silica glass that contains pores with a specific size distribution. Porous glasses can be made into a wide range of geometric forms (such as frit, rods, plates, beads, and hollow spheres), and pore sizes can be precisely tuned from the range of angstroms to millimeters. Controlling pore size means that the physical and chemical reactivity of the glass with gases and liquids can be tailored to specific applications such as chromatography, sensing, and filtering.
In addition to this, porous glasses exhibit high mechanical strength, chemical durability, and thermal stability; which make them superior to other porous media (such as polymers and ceramics) for a variety of applications.1
This article covers how porous glass is made, how pore size can be controlled, and some of the varied applications of this unique material.
Manufacturing Porous Glass
Porous glass can be manufactured via several different routes, each of which produces different characteristic pore structures. The most common methods involve phase separation or immiscibility of alkali borosilicate glass.
Producing controlled pore glass via the alkali borosilicate system
Alkali borosilicate glass systems consist of a silica glass-former with borate and alkali-oxide additives used to lower the melting temperature of the mixture and impart other properties. In other terms, alkali borosilicate systems are mixtures consisting of the chemical species SiO2, B2O3, and R2O; where R is sodium, potassium, or lithium.
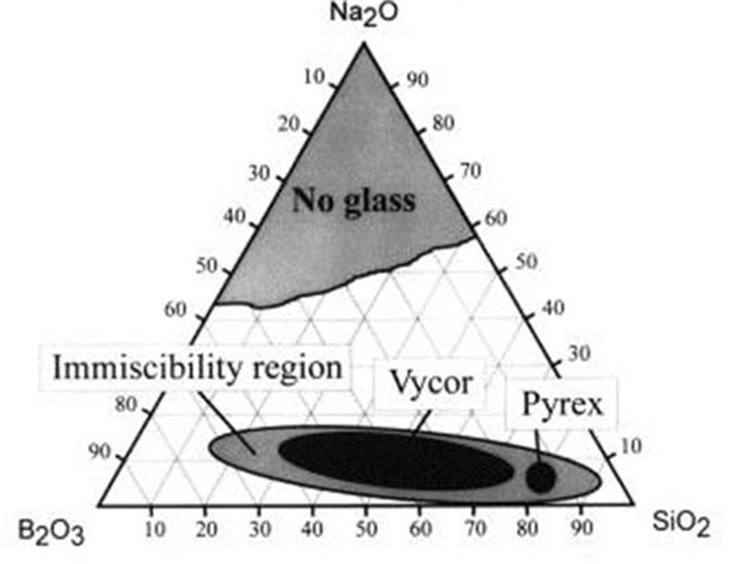
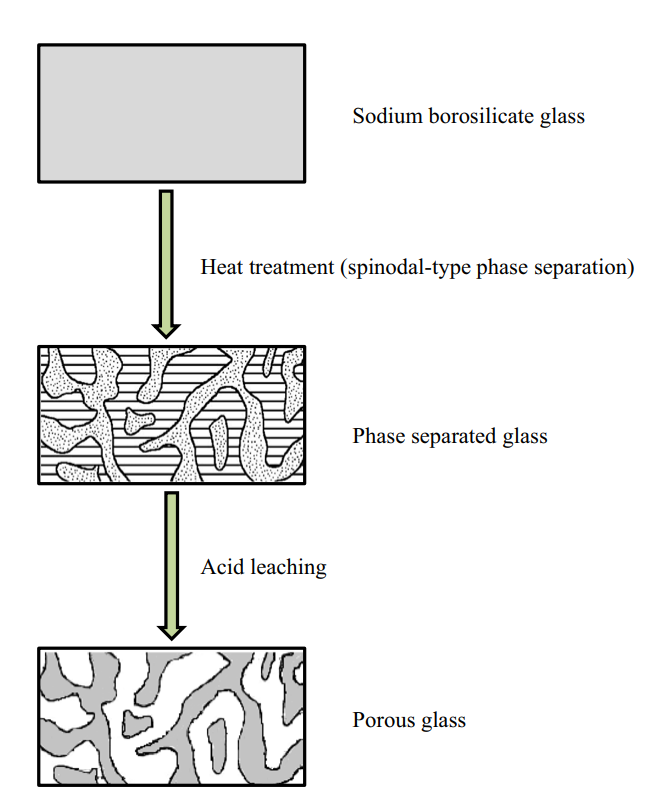
When the constituents of this mixture are tuned to specific concentrations and heated, the entire mixture undergoes an amorphous phase separation: the mixture transforms into two distinct phases.
One of these phases is an alkali-rich borate phase and the other a silica-rich glassy phase. Crucially, the borate phase is soluble in acid, while the silica phase is not. This means that, following heat treatment, the borate phase can be leached out with a hot acid solution. What remains is a highly pure and porous silica glass skeleton with large surface area: in other words, porous glass.
Controlling pore size
Acid-leaching of a phase-separated mixture generally results in a very narrow pore size distribution, earning the name “controlled-pore glass” and lending the resulting glasses to applications such as adsorptive chromatography of biomolecules.2
The average pore diameter is a function of heat treatment temperature and time, as well as glass composition. Thus, controlling the heat treatment temperature or time (or both) can easily produce porous glasses with a range of pore sizes to suit different applications. Glasses formed via these methods generally have pore diameters in the region of 1 to 1000 nm.3,4
Formation of porous glass using alkali borate systems can also be achieved without inducing a high-temperature phase separation: directly etching the surface of the glass can result in the formation of small pores (1-2 nm) restricted to the surface of the glass.
Other manufacturing routes
Porous glass can also be manufactured by glass sintering or via sol-gel routes. Glass sintering is widely used to produce glass foams with pore diameters in the region of 400 m to 1 mm. In sol-gel processes, a solution of organic monomers (sol) is turned into a glass by removal of the liquid phase. Sol-gel processes have been used successfully to create a range of pore sizes for different applications5,6 and they are becoming more common methods.
Applications of Porous Glasses
Porous glass provides an alternative to fused quartz which is comparatively difficult to produce and form into different geometries. However, many emerging applications make use of the functionality offered by the pores themselves. The high surface area and tailorable pore size distribution of these glasses make porous silica a highly effective filtering material, capable of separating not only the basis of molecular size but also of molecule type.7 This, along with a wide range of possible geometries, has made them useful in biosciences and chemistry.1
For example:
- Enzyme immobilization and size exclusion chromatography techniques have been developed using porous glass; making use of its extreme chemical inertness, optical transparency, and small pore diameters.5,8,9
- Surface-functionalization of controlled-pore glass using polyaniline has been used to develop optical chemosensors.10
- Using additives to finely tune the size of pores can result in functional size-selective catalyst supports.11,12
- The role of porous glass in targeted drug delivery has been studied, using porous-wall hollow glass microspheres. The spheres provide a porous, inert shell for the introduction and release of drugs inside the body.13
- Porous glass is also being investigated as a bio-scaffold. These applications make use of the porosity, strength, corrosion-resistance, and biocompatibility of porous glass.14,15
All of these applications are made possible by the tunability of pore size, which enables specific physical properties to be imparted in the glass during the manufacturing process.
Mo-Sci produces high purity (> 98% SiO2 and < 2% B2O3) porous glass frit and spheres suitable for applications in industry and research. Contact us to speak with one of our experts about your project requirements.
References and Further Reading
- Hasanuzzaman, M., Rafferty, A., Sajjia, M. & Olabi, A.-G. Production and Treatment of Porous Glass Materials for Advanced Usage. in Reference Module in Materials Science and Materials Engineering (Elsevier, 2016). doi:10.1016/b978-0-12-803581-8.03999-0
- Elmer, T. H. Porous and Reconstructed Glasses. in Engineered Materials Handbook (1992).
- Zhu, B. et al. Synthesis and Applications of Porous Glass. J. Shanghai Jiaotong Univ. 24, 681–698 (2019).
- Enke, D., Janowski, F. & Schwieger, W. Porous glasses in the 21st century-a short review. Microporous Mesoporous Mater. 60, 19–30 (2003).
- Lubda, D., Cabrera, K., Nakanishi, K. & Minakuchi, H. SOL-GEL PRODUCTS NEWS Monolithic HPLC Silica Columns. Journal of Sol-Gel Science and Technology 23, (2002).
- Baino, F., Fiume, E., Miola, M. & Verné, E. Bioactive sol-gel glasses: Processing, properties, and applications. Int. J. Appl. Ceram. Technol. 15, 841–860 (2018).
- Hammel, J. J. & Allersma, T. United States Patent | Thermally stable and crush resistant microporous glass catalyst supports and methods of making. 923, 341 (1975).
- Du, W. F., Kuraoka, K., Akai, T. & Yazawa, T. Effect of additive ZrO2 on spinodal phase separation and pore distribution of borosilicate glasses. J. Phys. Chem. B 105, 11949–11954 (2001).
- Jungbauer, A. Chromatographic media for bioseparation. Journal of Chromatography A 1065, 3–12 (2005).
- Sotomayor, P. T. et al. Construction and evaluation of an optical pH sensor based on polyaniline-porous Vycor glass nanocomposite. in Sensors and Actuators, B: Chemical 74, 157–162 (2001).
- Takahashi, T., Yanagimoto, Y., Matsuoka, T. & Kai, T. Hydrogenation activity of benzenes on nickel catalysts supported on porous glass prepared from borosilicate glass with small amounts of metal oxides. Microporous Mater. 6, 189–194 (1996).
- Gronchi, P., Kaddouri, A., Centola, P. & Del Rosso, R. Synthesis of nickel supported catalysts for hydrogen production by sol-gel method. in Journal of Sol-Gel Science and Technology 26, 843–846 (Springer, 2003).
- Using Porous Glass Microspheres for Targeted Drug Delivery Mo-Sci Corporation. Available at: https://mo-sci.com/porous-glass-microsphers-targeted-drug-delivery/. (Accessed: 2nd September 2020)
- Rahaman, M. N. et al. Bioactive glass in tissue engineering. Acta Biomater. 7, 2355–2373 (2011).
- Fu, Q., Saiz, E. & Tomsia, A. P. Bioinspired strong and highly porous glass scaffolds. Adv. Funct. Mater. 21, 1058–1063 (2011).